Test stands: High pressure monitoring – safe and reliable
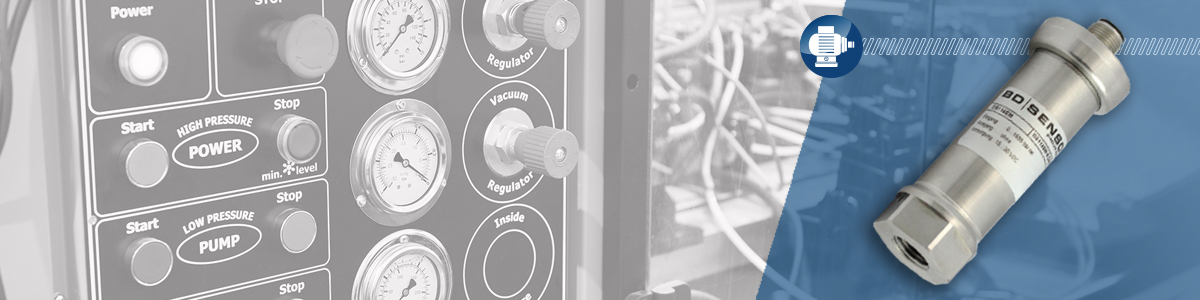
The requirements on modern machines and equipment are constantly rising. Diverse sensors, actuators, electrical and mechanical components ensure reliable functionality and safe operation. The focus isn’t always on rotating or sharp-edged parts. Protection against high surface temperatures and pressures is equally important.
APPLICATION
For lifting units or hydraulic test stands it is important that safety devices only permit access to the system if these are in a virtually depressurised state and so the system pressure needs to be continuously monitored to release doors, covers etc.
The electronic pressure switch DS 114EM was devised to perform this critical task safely and reliably. It is designed in the customer application for monitoring a process pressure of 1,700 bar.
IMPLEMENTATION
Its precision switching electronics enables safe switching functionality even at low switching thresholds. This is where the advantages of this pressure switch are particularly apparent because besides the conventional hysteresis mode in which the switching hysteresis defines the switch-on and switch-off point, it is also possible to specify a switching range to carry out pass/fail monitoring. Which means, for example, that all pressure values within the switching thresholds e.g. are acceptable and the system emits an error signal if the pressure value goes outside of these thresholds.
Another key feature is the integrated potential-free switching contact as electronic pressure switches generally have a PNP or NPN switching output with a galvanic reference to the supply voltage. The lack of potential makes it possible to directly use the switching signal to control other switching components or signal transmitters without having to consider the potential ratios.