Propulsion technology: regulation of working pressure in tunnel boring machines
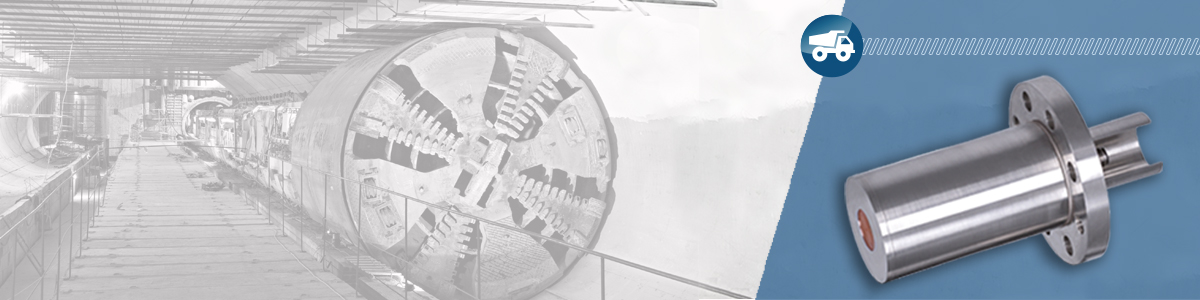
London, Shanghai, New York City – what do all these metropolises have in common? More and more people move to megacities to comply with job requirements and to fulfill their personal dreams of a perfect work/life balance. As the horizontal usage of land quickly finds its natural limits, new buildings need to be designed as tower blocks, and new infrastructure for traffic and supply purposes must run underground.
APPLICATION
Tunnel boring machines (TBM) are the basic equipment here. A TBM consists in principle of a pressurized excavation chamber, which is used for the actual boring process, and of a separation plant for the excavated material, which is under atmospheric pressure. A bulkhead separates both chambers and controls the pressure in between using pressure sensors.
Excavation tools remove the soil, whereas bigger rocks need to be cut into smaller stones first. This mixture of water and solid material creates a support pressure in the excavation chamber, controlled by either a screw conveyor or a slurry circuit:
- The screw conveyor transports the removed soil to the back of the unit. The rotation speed of the screw conveyor controls the support pressure.
- The slurry circuit is a hydraulic support that transports the slurry suspension (with an adjustable air cushion) to the excavation chamber and the mixture of suspension and removed soil back to the separation plant.
Hydraulic cylinders push the machine forward for the segmental lining of the tunnel. This lining method provides a high degree of security for the tunneling team as well as for the future tunnel stability.
IMPLEMENTATION
Industrial pressure measurement is faced with the following challenges here:
+ During the boring process, many solid particles (sand/clay/gravel) mixed with water come into contact with the transmitters, and can easily destroy standard stainless steel and ceramic diaphragms by local overpressure and abrasion.
OUR SOLUTION
We use a ceramic sensor element in combination with an elastomer diaphragm.
+ Sedimentation in front of the diaphragm can cause imprecise measurement
results and damage.
OUR SOLUTION
The totally front-flush diaphragm is fixed inside a tube; the transmitter is mounted on the backside of the bulkhead to eliminate dead spaces.
+ The very close proximity to the driving and cutting part of the TBM causes strong and permanent vibrations.
OUR SOLUTION
The entire construction of the pressure transmitter unit is extremely robust.
The housing walls are considerably reinforced, and an exchangeable “cage” is installed around the electrical connection as an extra protection.